When it comes to shipping goods and ensuring their safe transportation, mastering the art of packaging becomes essential. And in this realm, pallet wrappers and stretch wrap machines play a pivotal role. These remarkable devices have revolutionized the way items are secured on pallets, providing efficiency, stability, and protection throughout the entire shipping process.
A pallet wrapper, also known as a stretch wrapper, is a versatile tool that automates the task of securely wrapping products or goods onto pallets. By utilizing stretch wrap film, it tightly binds the items together, creating a unified and stable load. This not only prevents product damage during transit but also enables efficient utilization of storage space.
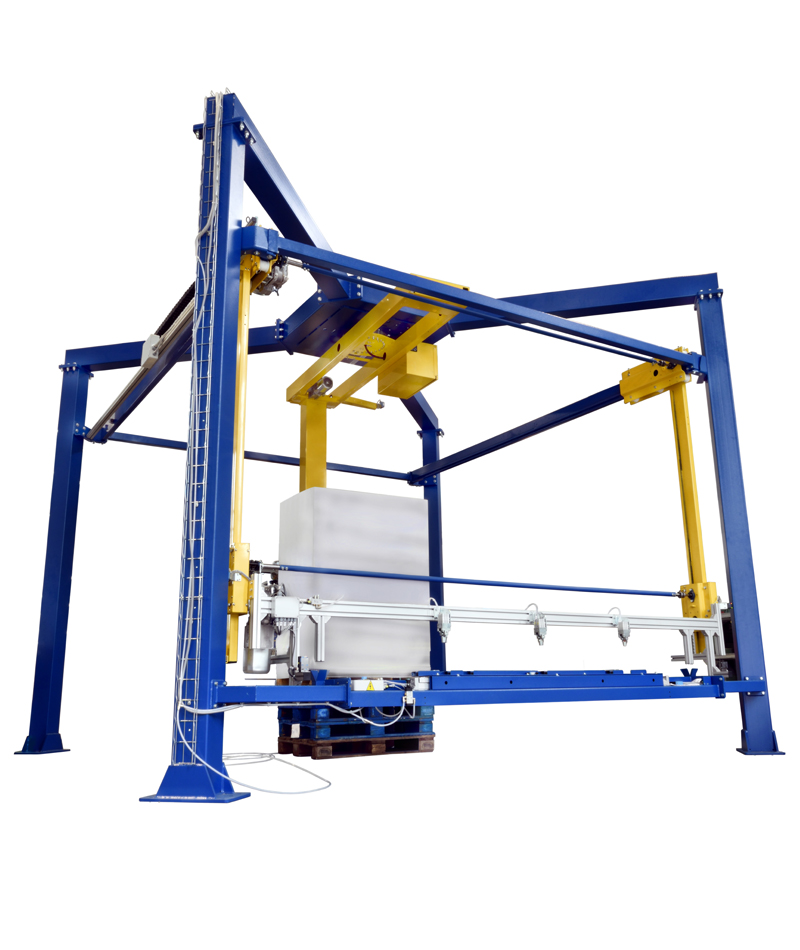
Stretch wrap machines, on the other hand, offer further advancements in packaging technology. These powerful devices automate the entire wrapping process, eliminating the need for manual labor and ensuring consistent results every time. Equipped with innovative features such as adjustable tension controls, automatic film cutters, and programmable settings, stretch wrap machines streamline operations and enhance productivity.
By incorporating pallet wrappers and stretch wrap machines into packaging workflows, businesses can benefit in numerous ways. Firstly, these machines save time and reduce labor costs, allowing personnel to focus on other crucial tasks. Additionally, the consistent and uniform wrapping provided by these devices ensures greater load stability, reducing the risk of damaged goods and minimizing potential losses.
In conclusion, pallet wrappers and stretch wrap machines have become integral tools in the world of modern packaging. Their ability to securely bind items onto pallets, streamline operations, and enhance transportation safety makes them an indispensable asset for any business involved in shipping goods. By mastering the art of utilizing these machines effectively, businesses can enjoy increased efficiency, reduced costs, and most importantly, peace of mind knowing their products are well-protected throughout the entire journey.
Benefits of Pallet Wrapping Machines
Pallet Wrapping Machines offer a range of benefits, making them an essential tool for efficient packing and transportation. These machines provide several advantages that help streamline the packaging process and protect goods during transit.
Firstly, pallet wrapping machines ensure optimal stability and load security. By tightly securing the stretch wrap around the goods, they prevent any shifting or movement during transportation. This eliminates the risk of product damage, reducing the chances of loss and increasing customer satisfaction.
In addition to enhancing load stability, these machines also save time and labor. With their automated functions, pallet wrapping machines efficiently wrap pallets in a fraction of the time it would take manually. This allows workers to focus on other tasks and increases overall productivity in the warehouse or distribution center.
Moreover, pallet wrapping machines contribute to cost savings in the long run. By providing consistent tension and minimizing the amount of stretch wrap used, they help reduce material waste. This not only helps decrease packaging costs but also promotes sustainability by reducing environmental impact.
Overall, investing in a pallet wrapping machine brings numerous benefits to businesses involved in packaging and transportation. From ensuring load security and saving time to reducing costs and promoting sustainability, these machines are a valuable asset in mastering the art of packaging.
Choosing the Right Stretch Wrap Machine
When it comes to selecting the perfect stretch wrap machine for your packaging needs, it’s important to consider a few key factors. First and foremost, you should evaluate the size and volume of your operation. This will help determine whether a semi-automatic or fully automatic stretch wrap machine is the best fit for your business.
Another crucial aspect to consider is the type of load you will be wrapping. If you primarily deal with uniform loads, a turntable stretch wrap machine might be the most suitable option. On the other hand, if your loads vary in shape and size, an orbital or rotary arm stretch wrap machine would offer the flexibility needed to effectively secure your products.
Additionally, it’s essential to assess the desired level of automation and control. Depending on your requirements, you may prefer a stretch wrap machine that allows for adjustable wrap tension, various wrapping patterns, and adjustable film carriage speeds. These features can greatly enhance efficiency and ensure optimum performance for your packaging operation.
In summary, the key to choosing the right stretch wrap machine lies in understanding your specific needs and considering factors such as the size and volume of your operation, the type of loads you handle, and the level of automation and control required. By carefully evaluating these factors, you can find the perfect stretch wrap machine to streamline and enhance your packaging process.
Stretch Wapper
Optimizing Stretch Wrapping Techniques
In order to achieve optimal results with your stretch wrapping process, it is important to employ effective techniques. Here are some key considerations to keep in mind:
Pre-Stretching for Enhanced Load Stability: Utilizing a pallet wrapping machine equipped with a pre-stretch unit can significantly improve load stability. This technique involves stretching the film before it is applied to the load, allowing it to better conform to the shape of the products and securely hold them in place. By maximizing the film’s stretch potential, you can minimize the risk of load shifting during transportation.
Choosing the Right Film for the Job: Selecting the appropriate stretch wrap film is crucial for achieving desired results. Factors such as load weight, size, and shape, as well as transportation conditions, should all be taken into consideration. Different films have varying levels of stretch, puncture resistance, and cling properties. By understanding your specific packaging requirements, you can choose a stretch film that best suits your needs and optimizes the protection of your products.
Implementing Consistent and Uniform Wrapping Patterns: Consistency in wrapping patterns plays a vital role in load stability and overall packaging efficiency. By following a uniform wrapping pattern, you can ensure that the entire load is adequately secured and that there are minimal weak points in the wrapping. Whether it’s the classic spiral pattern or a modified method like cross-hatching, the key is to apply the film evenly and tightly throughout the entire load.
By incorporating these optimization techniques into your stretch wrapping process, you can enhance load stability, minimize the risk of damage, and ultimately maximize the efficiency of your packaging operations. Remember to evaluate your specific requirements and adapt these techniques accordingly for the best results.